Road-rail milling truck:The universal genius
×
- Transport truck and machine in one
- Simple logistics & ideal for small-scale works and tram networks
- Transfer via road or rail
- Maximum mobility and flexibility
- Simple on-railing & off-railing – right at the work site where possible
- Short tooling times
- Entire profile machined in just a single pass
- Finish grinding thanks to integrated grinding equipment
- Minimal dust and sparks produced
- Dismantling of trackside switching and signaling equipment is not required
- Variable track gauge from 1,000 to 1,520 mm
- Switch processing from 1,435 to 1,520 mm possible
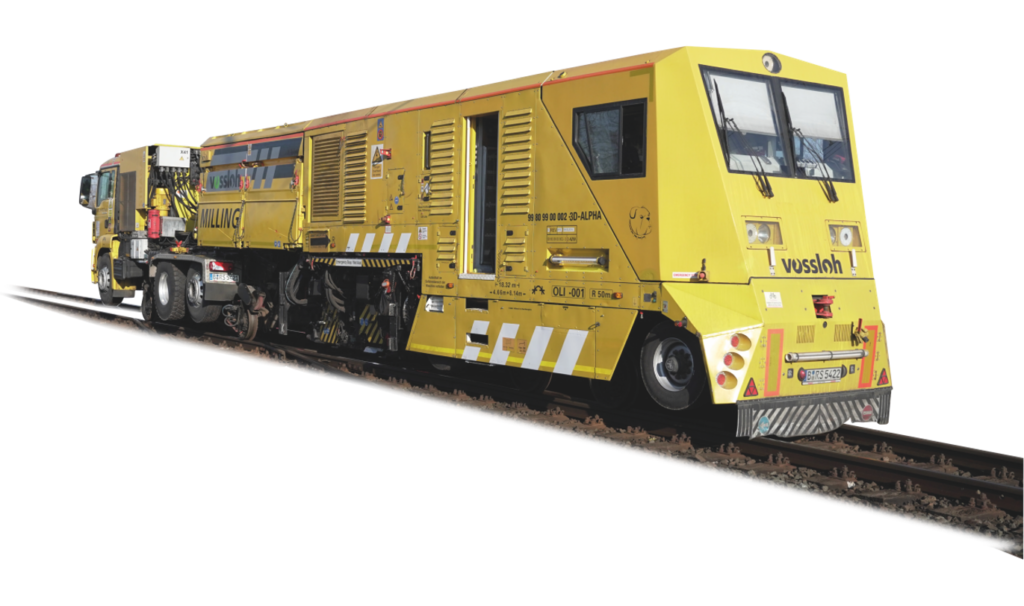
Milling grooved rails to reduce noise
- Significant reduction in noise emissions through the removal of corrugations
- Grooved rails fully reprofiled for the first time thanks to new milling wheel – and without removing the gap sealant
- Removes larger amounts of metal including from the bottom of the groove towards the gauge corner
- Milling of grooved rails with hardened rail heads and gap sealant
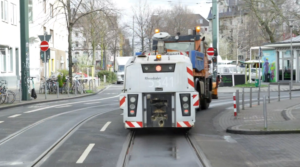
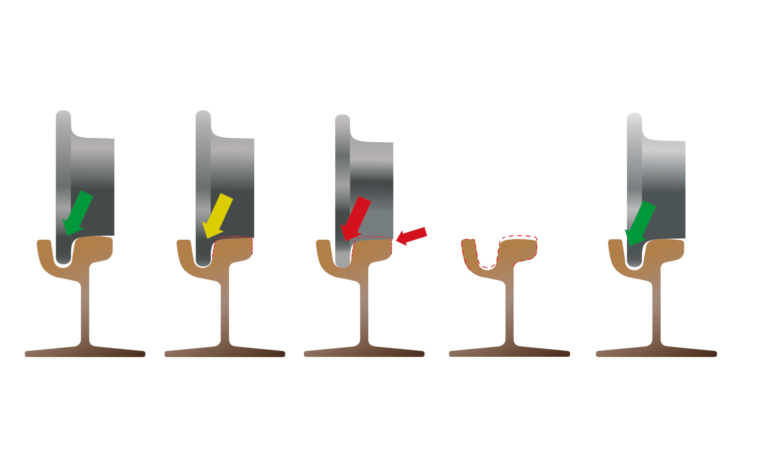
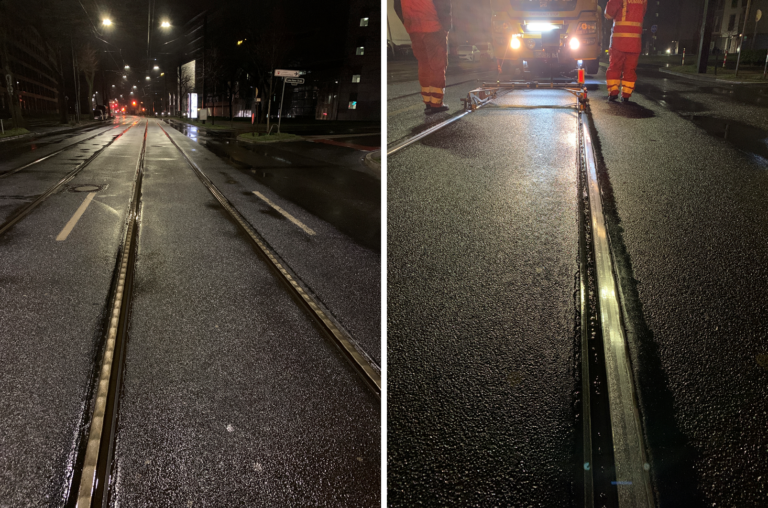
Side gouging in curves
- The damage to rails that have always been replaced because of deep gouging can now be milled out.
- A specially developed millling wheel relocates the critical zone approx. 4 mm below the side gouging.
- Applications: side gouging in curves
- The lower rails of curves can sometimes have severe burring, which is also removed
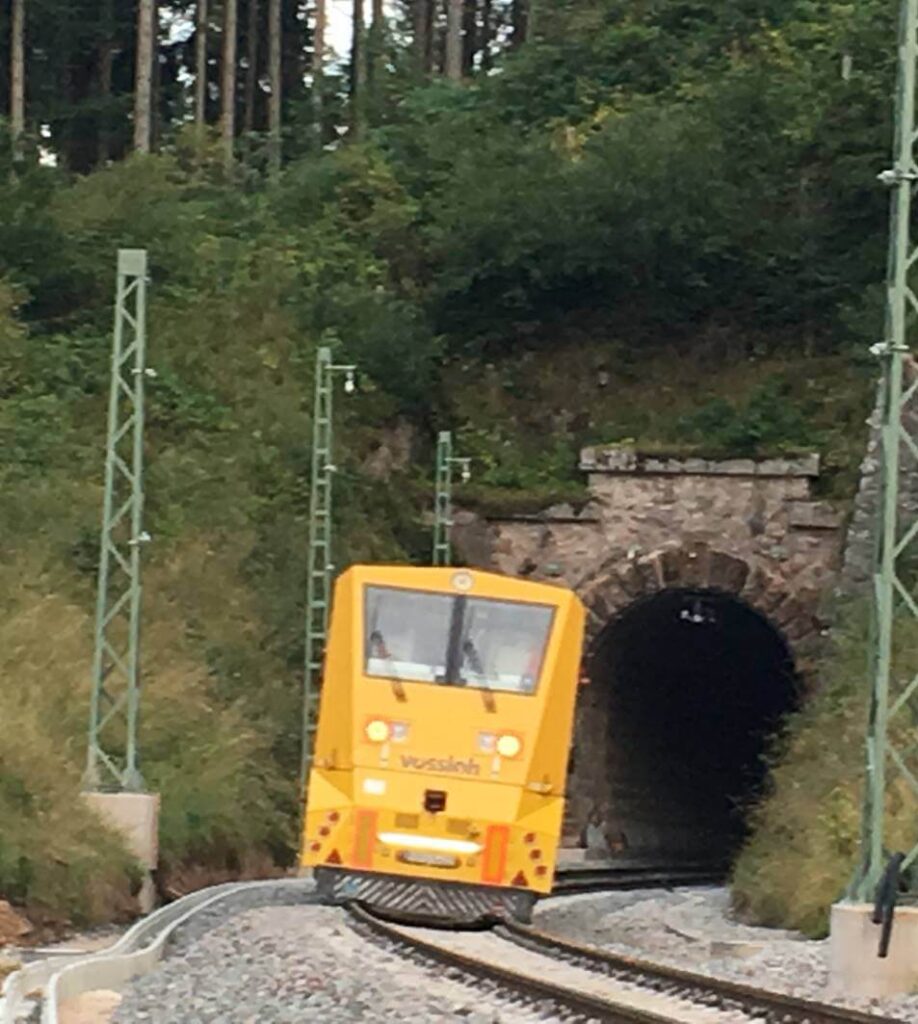
Switch machining (Vignole rails)
- Complete reprofiling of the mainline and the turnout including frog, wing rails and points down to 20 mm width
- Minimal time required for machining
- Reprofiling returns the switch to near-new condition
- All switches with spring-action frogs can be machined
- Not recommended for economic reasons: single-slip switches, double-slip switches and crossings
Thanks to a specially constructed tool and some adjustment of the software for the machining process, it’s possible to mill more than 95% of a switch including its wing rails, the frog and the points. Grinding with the Flexis System, specifically designed for the maintenance of switches, is then only required for the alignment work in the transition zones.
Milling level crossings
- The tool on the SF02 road-rail milling truck has the same dimensions as a rail wheel, which allows it to machine rails all the way through a level crossing.
- Clearance at the gauge corner complies with the European standard for wheel flanges: 38 mm laterally and a width of 42 mm
- Ideally, the adjacent material should be 2 mm lower than the top of the rail.
- The rail that has been damaged by the grit put down in winter is completely reprofiled.
Track gauge correction
- Avoids having to close tracks to traffic
- Prevents premature wear of the vehicles’ rail tyres
- Reduces noise emissions and improves operational safety
- Applicable wherever burring or flexural fatigue in the sleepers can cause gauge narrowing