In the new lead factory for rail fastening systems, existing processes were streamlined & optimized and new processes were integrated to achieve an increased sustainability over the entire value chain. In the analysis and the setup of the new production layout, we leveraged all our metal working experience. Our plants operate at optimum efficiency and we continuously keep an eye on improving the energy efficiency and using resources in an environmentally friendly way. Thanks to Vossloh‘s technological know-how and in-house tool development, the capacity of the new factory is globally unrivalled.
Digitalized processes for an enhanced customer service
Today, customers from more than 90 countries rely on our sophisticated and high-quality products which enable them to focus on essential infrastructure responsibilities. Our Manufacturing Execution System (MES) controls the fully automatic production process, and this automation contributes to data transparency. All data are consistent and available in real time – from ordering via our eCommerce platform through to the shipment.
- The order data define quantity, type of steel, bending geometry, treatment, hardening & tempering as well as the selected kind of packaging.
- Since order data and production are linked together, the material flow in the chained production line is clearly controlled (e.g. order for coated or uncoated tension clamps).
- The related steps in the respective stations are fully automated. Digital control and monitoring of the process provide end-to-end production security and traceability.
We use this pooled potential for a faster and more reliable processing of orders and more flexibility in our response to customer wishes.
read more
read less
Our tension clamps are produced from up to 100 % recycled raw material, which is supplied in the form of wire coils from steel works in Germany or the EU. In order to impart the desired properties to this raw material, the steel wire is run through a multi-step, fully automated production process.
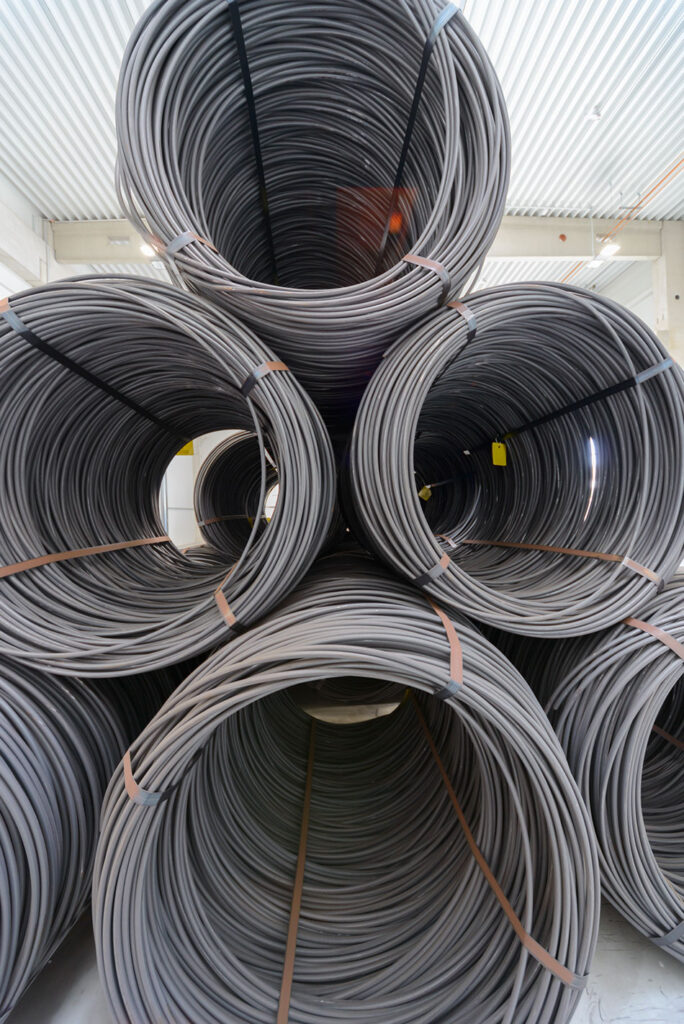
The pickling alone comprises eight stages. In a succession of several baths, the steel surface is cleaned and rust is removed.
- Treatment vat capacity of the hydrochloric acid tanks reduced by 35 %
- Pickling at ambient temperature
- Wetting the wire with a lime cover to prevent corrosion & ensure optimum adhesion of oil on the wire surface during the bending process
- Lime bath at 85 °C; indirect heating/steam
- Plant encapsulation & air washer (optimization of the working conditions, reduction of wear and tear, avoidance of hazardous emissions)
- State-of-the-art effluent treatment
Straightening, cutting to length and bending of the tension clamps in one production line:
- During straightening & cutting to length, the wire is uncoiled, straightened and then cut into dimensionally specified bars so that in the next process step – bending – the tension clamp can be bent via individual presses and a handling robot system.
- In the processes of straightening & cutting to size, the wire is unreeled, straightened and then cut into dimensionally specified rods so that in the next process step the tension clamp can be bent using individual presses and a handling robot system.
- Rotary system for robot-assisted throughput
- Tension clamps are then placed separately on frames, rather than being deposited as bulk in steel containers. This way, every individual tension clamp can be identified, counted and handled separately.
- Before the hardening & tempering, the tension clamps are washed to remove the oil that had been applied for the bending process.
- Total plant capacity unique in efficiency & performance worldwide
- Faster processing with smaller footprint
- High production reliability
To achieve the ideal balance of hardness and elasticity, the hardening and tempering process is performed in continuous belt furnaces. The balanced microstructure of the metal and the desired quality are ensured through the right sequence of twice heating (in the furnace) and cooling (in the dipping bath).
When they have cooled down to ambient temperature, the tension clamps in their multilayer frames are scanned by another handling robot. Based on the scanning result, the tension clamp packs are then either conveyed for further processing (coating) or packaged in the ordered quantity for the direct shipping to the customer.
Quality inspection of each batch:
- Fluxing of the tension clamps (crack test)
- Vickers hardness measurement
- Dimensional test, recording the spring characteristic curve
More energy efficiency
With the smart factory, we have aimed for environmentally friendly production with a significantly improved CO2 footprint, and ultimately achieved this.
New burner technology
Heating of incoming combustion air using outgoing waste gases
- Significantly reduced temperature of the generated waste gases
- Increased burner management efficiency
New insulation
Installation of optimum insulation in the new high-temperature furnace
- Lower heat losses
- Energy savings
- Reduced emissions
Waste heat utilization
- Waste air heat from afterburning is guided directly to the outside thorough a duct network.
- Along the way, heat from the waste air stream is transferred to the circulating oil and water via heat exchangers.
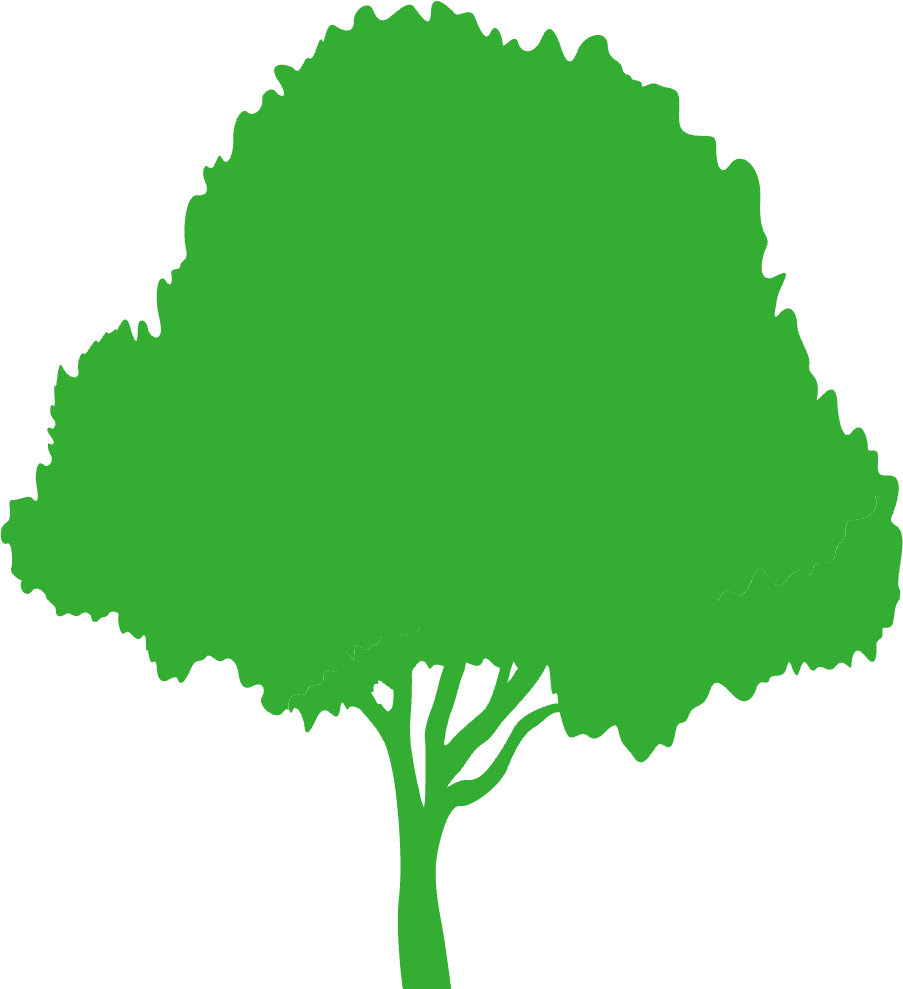
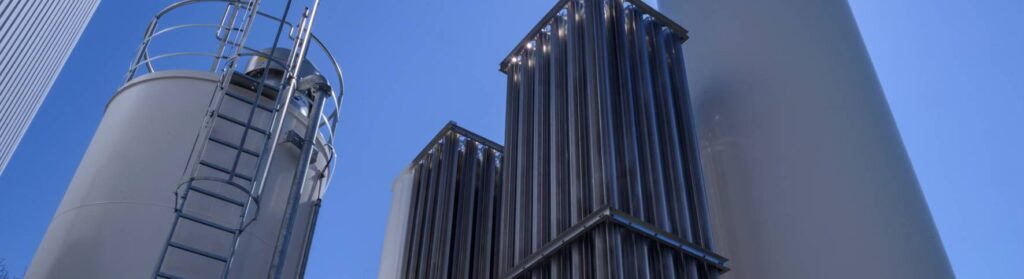
The coating of tension clamps is an optional step.
By combining the production with the separation, i.e. the singling & stacking of the tension clamps, and with the Vossloh protect coating – our premium corrosion protection – we have shortened the processing time for our tension clamps.
- Coating line for Vossloh protect with highest possible efficiency level
- Application process guarantees exclusion of production-related hydrogen embrittlement
- Efficient use of resources due to low coating thickness
- Special customer requests can be met with the top coat, and tension clamps can be color-coded for their special area of application
- No environmentally harmful chemicals such as chromium compounds and heavy metals are used in the production process
Alternative coating processes are still performed by external partner companies.
All from a single source: High value creation through vertical component integration
Also the integration of plastic and EPDM components by in-sourcing their production has had a positive impact on delivery periods and transport activities as a whole.
- Six injection moulding machines based on Vossloh’s own injection moulding technology are available for the production of angled guide plates and dowels.
- Our production lines for the highly elastic cellentic components (rail pads & intermediate plates) are located in Lüdenscheid, where also our central warehouse is situated.
cellentic: nitrosamine-free EPDM compound
- Carbon emissions reduced by >10 % over the entire lifecycle
- Ecological further development with eco-friendly vulcanization accelerators
- Healthier cycle in production and in the track
- Product range of rail pads & intermediate plates available as series products and as tailored individual solution
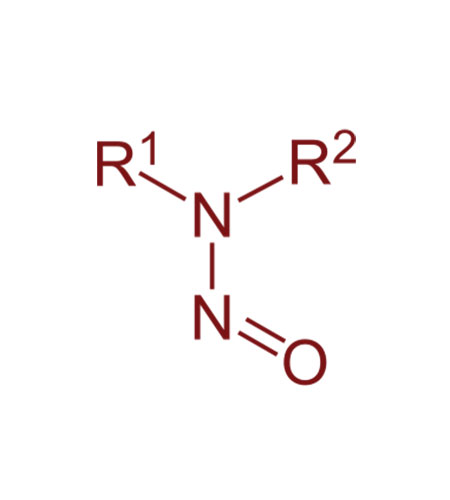
Nitrosamines are chemical reaction products that mainly occur under the influence of heat. They can be found - albeit in only small doses - in food & beverages, cosmetics and toys.
read more
read less
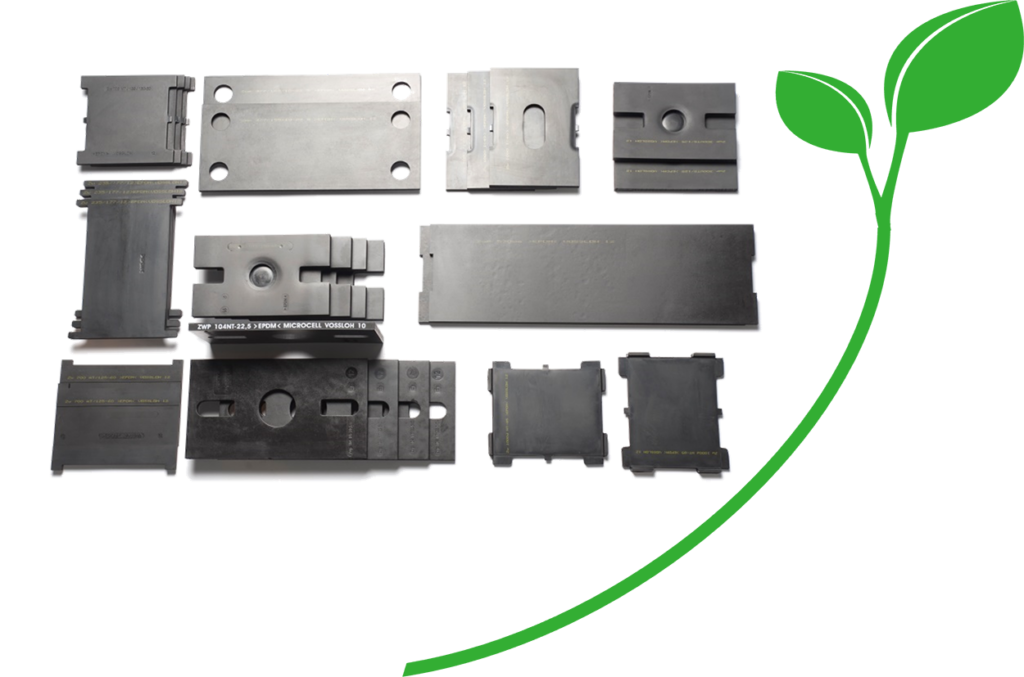
Sustainable transport all over the world
The stacked tension clamps and the fastening components are shipped all over the world either directly or via the own logistics centre using various packaging systems.
A novelty is our Smartbox for the parties to our framework contract in Europe. This eco-friendly reusable packaging box not only offers a better protection of the product but also allows an ergonomic component removal. When the Smartboxes are empty, they can be folded so they have only half the volume during storage and return shipping. With the Smartbox, we close the value creation cycle with our customers..
Capacities for innovation at the Werdohl site: The Technology Centre
Vossloh’s innovative strength will benefit from the proximity of the Factory of the Future to the Technology Centre:
- Extension of our capabilities to meet application-specific requirements of our customers
- Optimized development process from the idea to the marketable innovation
- Well-equipped development offices and laboratories with their own mobile measuring systems
- State-of-the-art fleet of testing machines for quality control
- Possibility of simulating material tests or continuous load tests or performing real-life tests for tailored product modifications.
Setting international standards
- Cooperation with regulators worldwide in developing and improving their technical regulations
- Close cooperation with over 20 renowned universities, institutes and engineering firms
- Research & development on the effects of increasing track loads and the resulting wear of track components
- Focus on issues such as reduction of noise and vibrations through the use of innovative materials for fastening components as well as their interaction in the overall system
- Pilot facility for development of amalentic and new EPS sleepers
- The technological and organizational infrastructure consolidates and integrates the company’s expertise.
- Our aim: setting international standards that ensure the safety of track even under extreme conditions.