Mobile flash-butt welding: Quality through processor-controlled precision process
Fully automatic welding process
- Flash butt welding is one of the most advanced technologies for producing a seamless track body. As in stationary long rail welding, the rail ends are heated by high-amperage resistance heating up to the required welding temperature and are subsequently pressed against each other at a high hydraulic pressure – without the introduction of any foreign material.
- As a result of our processor controlled, fully automatic flash-butt welding process, these welded joints are less prone to failure and ensure a significantly higher strength and durability.
- On the process and machine side, we have numerous country approvals as well as sufficient capacity to successfully complete major construction sites, such as on the high-speed rail lines in Germany, as well as the Follobanen tunnel project in Norway, on schedule.
The various work steps of the flash-butt welding process, taking into account the direction of work
Rail neutralization with hydraulic rail pulling device
Fine grinding
- Rail grinding machines (optional – hydraulic rail bender)
- 2 workers
Tightening rail fastenings
- 2 power wrenches or clip machines
- 2 workers
Continuously welding rails
- Flash-butt welding machine
- 1 operator, 1 worker for rough grinding
Neutralization with rail-pulling device
- Anchoring rails and pulling the required distance
- 2 worker (pulling)
- 4 workers
Anchoring rails and pulling the required distance 2 worker (pulling) 4 workers
- Excavator with rail carrying tongs
- 1 driver/operator
Contact grinding & cutting rails (joints between the sleepers)
- 1 rail cutting machine
- 1 angle grinder
- 1 power station
- 2 workers
Loosening rail fastenings
- 2 power wrenches or clip machines
- 2 workers
Fields of application of our mobile welding trucks
Advantages and limits of use compared to other welding methods
- Higher quality & strength (about 500 kN greater bending force compared to thermite welding for rail profile 60E1)
- Greater process stability & high reproducibility of the result in mass production due to processor control ¨ No additional ultrasonic testing required
- High quantities in a short period (up to 8 welds per hour) for fast work progress
- No foreign materials are employed > much safer working conditions & more environmentally friendly:
- significantly less smoke and dust
- considerably less waste, which is also recyclable
- no slag or welding residues
- no mold or packaging etc., only the sheared bead
- reduced logistical effort
- Applicable irrespective of weather conditions
- Can be used worldwide:
- Ambient temperature from -10 to +55° C
- Maximum working altitude up to 3,000 m above sea level
- Our machines cannot be used in switches and for the final weld
- Our machines are not suitable for grooved rails
- Higher costs for certification and maintenance of the machine in the respective countries where it is used
- Personnel require higher qualifications (traction vehicle driver, truck license, certification as a flash-butt welding machine operator)
- According to technical specification, smallest radius ≥ 300 m
Follo Line:Key data on currently the largest railway infrastructure project in Norway
Tunnel length: almost 20 km, twin-bore (Norway‘s longest rail tunnel)
High-speed line: 250 km/h (connects Oslo with southern Norway)
Number of welds: 694 in just five weeks at the end of 2021
Shifts: 25 in just five weeks at the end of 2021
Only provider of flash-butt welding services in Norway
Vossloh is the only company with a machine procedure approval for Norway including the fatigue test method for testing welded rail joints in accordance with the EU standard EN 14587-2:2009-08 to qualitatively verify the minimum load-bearing capacity and standard deviation (carried out using the more exacting staircase testing method).
Highlight: currently Norway‘s largest railway infrastructure project
Sneltram Project in Utrecht: Semi-stationary welding
Improvement of the SUNIJ-Lijn to enable the use of low-floor trams
Due to very tight curve radii – typical for tram lines – three welding depots were set up for the production of long rails next to the work site
More than 850 welds
Reduced number of rail transports and field welds
Minimum time pressure & increased safety (fewer people on the track)
Highlight: nearly 60 welds within nine hours, which may be a record!
References on four continents
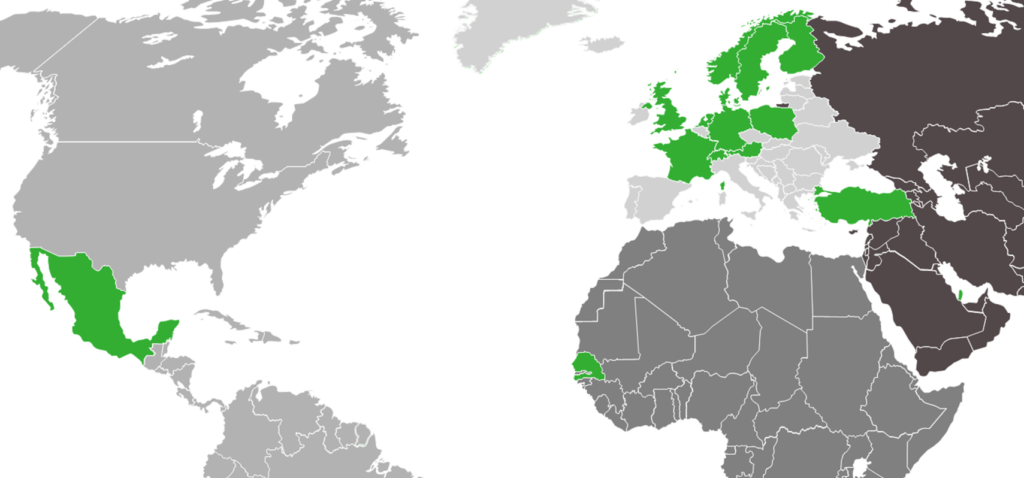