- Today, the maintenance of tram switches can be quite complex. Although the Flexis system, for example, enables precise rail maintenance of complete turnouts, including areas inaccessible to large machines, such as crossings and switch blades, with removals ranging from preventive to corrective (up to 1.5 mm), the replacement of crossings and the welding of individual defects in stock rails and switch blade supports are part of the standard turnout maintenance program.
- However, welding has an effect on the track, as an area around the turnouts must be cleared for preheating the rail head – e.g. by breaking up the coating/track embedding (asphalt surface) or a concrete slab or removing insulation or paving stones.
Vossloh's innovative approach
- Simple maintenance, with reduced intervention time and the minimum of resources to restore the points as close as possible to their original state.
- The innovative, patented tram switch enables all wear parts to be replaced.
- In addition, the customer can plan the replacement more easily due to its short maintenance period.
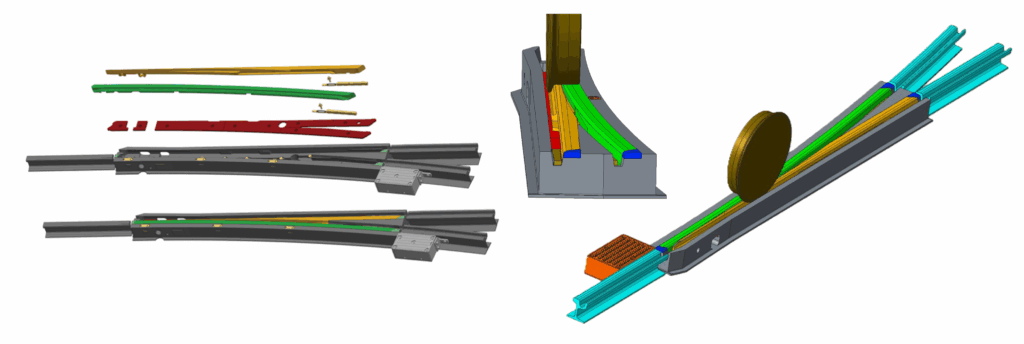
Advantages at a glance for maintenance engineers of tram networks
- From a quality point of view, there are no more repairs in the functional part during maintenance, as worn parts are replaced with new ones. This means that the proper functioning of the switch no longer depends on an almost manual reprofiling of the stock rail, which is achieved by welding on and grinding material. In particular, the connection between the switch blade and the stock rail is now guaranteed by new parts manufactured in the factory.
- From a logistical point of view, it is no longer necessary to break up concrete/asphalt, remove paving stones or insulation. All parts are accessible from the top of the turnout and welding is no longer necessary.
- Maintenance times on site are reduced by at least half. This time saving allows our customers to optimize schedules and avoid the need for alternative traffic during maintenance work.


- Higher quality results
- Flexibility in the choice of materials: As all components that come into contact with the wheel are interchangeable, the material can be adapted to the actual requirements on site at any time – even after installation. This means that a less hard and therefore less expensive material can be used in a depot or, conversely, a very hard material can be used for a heavily used turnout.
- Environmentally friendly: The simplicity of the maintenance work significantly reduces carbon dioxide emissions on site and noise pollution for local residents. In addition, today’s networks often have switch supports made entirely or mainly of high-strength steel, whereas in this new switch only the parts that come into contact with the wheel and the switch blade are made of high-strength steel. The rest, i.e. 80% of the new Vossloh switch, is made of normal steel, which further reduces the CO2 footprint.
- From a cost perspective, the power consumption for the switch heating is halved compared to a conventional switch. By optimizing the positioning of the heating elements inside the device, we avoid any contact between the heating system and the surface (concrete/asphalt) or insulation, thus removing any protrusion that could impact the coating or insulation.
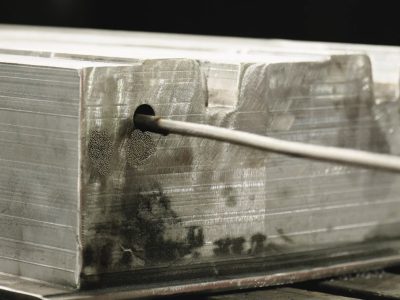
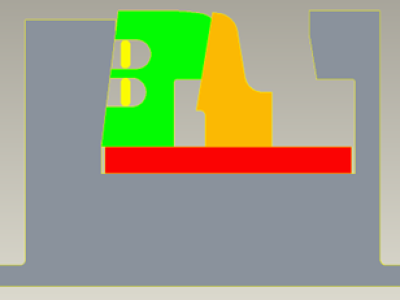

Qualification program
Modelling & Analysis: Through numerical simulation, study of fatigue and assembly deformation
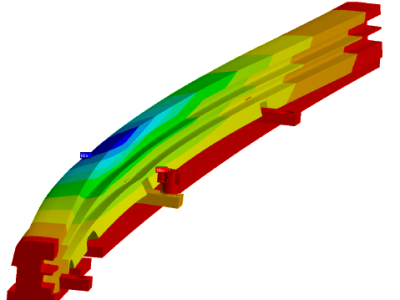


Permanent assembly qualification: Validation of operating procedures
Rail – 1/2 switch link
Reloading entry / Exit switch

Climate test: Simulation of device degradation to guarantee …

Corrosion test: … component interchangeability at all times
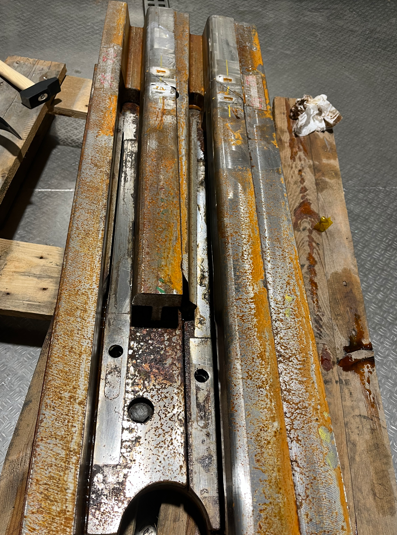
Fatigue test: Reproducing the wear and tear of material by subjecting the assembly to vibration, friction, acceleration and braking, as in a repeated passage of a tram wheel


Thermal efficiency:
Reduced energy input
Optimized heat flow


Availability – Maintainability – Safety: Study to estimate system performance throughout the life cycle

Monitoring Program: Intensive control operations to ensure the safe passage of the tramway

Putting the project on track – Charleroi, Belgium
On-site installation
As part of the replacement of an existing switch, we had proposed an installation with this new concept. This would be accompanied by a monitoring phase of 2 to 5 years, including a phase of replacement of the stock rail to finally validate the concept.

